Picking and Sorting: Case Study
Leclerc Drive : Large Retail
How E. Leclerc Drive Doubled Its Productivity While Reducing Strain for Its Pickers?
Client’s Needs:
Increase productivity
Address turnover among order pickers
Context:
The drive-thru service is a rapidly growing activity, operating in a competitive environment where recruitment and staff retention are challenging.
For Mr. Mailfert, the director of the operation, the main challenge when launching this drive was to achieve a high level of productivity, regardless of the experience of the order pickers, while also reducing workplace strain.
Challenges Faced:
- Limited productivity during the product picking stage
- Long training periods for new hires (around 3 weeks) due to the need to memorize routes and locations
- High workload: long routes for operators, backtracking, and time-consuming searches
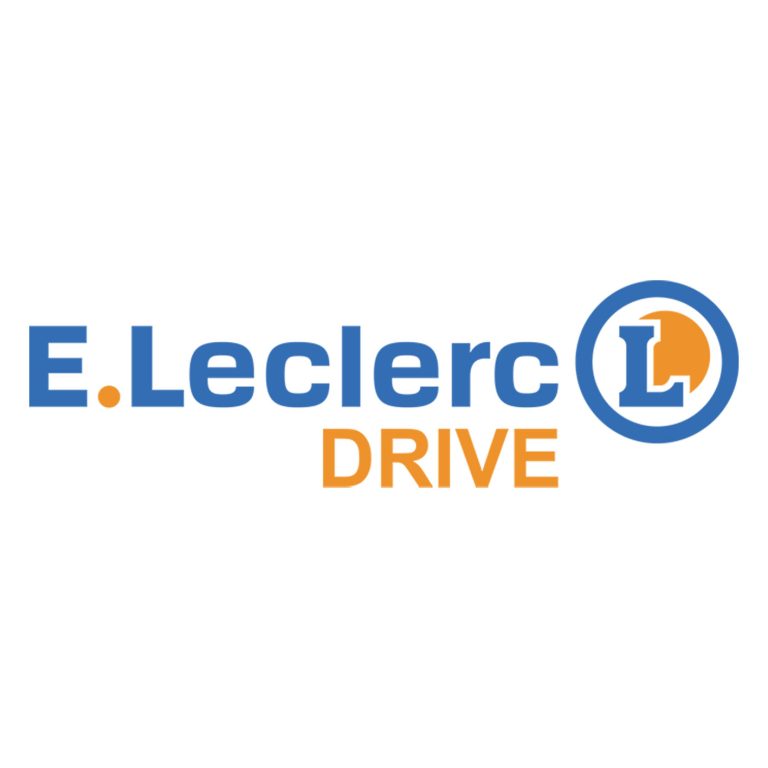
Our solutions:
Optimizing Picking and Sorting of Orders
Deployment of Our Picking and Sorting Software:
The Go-to-Light solution integrates Pickeos’ “Picking and Sorting” concept, allowing orders to be merged into a single preparation route (called Picking), after which a dedicated station handles the task of reconstructing customer orders. The solution was specifically configured for Leclerc Drive in collaboration with the retailer’s usual IT provider to optimize the number of orders, pre-sorting, and collection areas. This significantly reduces operator steps and increases productivity.
Implementation of LED Light Guidance:
The Pick-to-Light LED system saves operators time by instantly showing which products to pick, in what quantity, and for which sorting task. Pickeos enhances LED functionality with color, flickering, blinking, and quantity options. With LEDs, training time is reduced, and operators experience less fatigue when searching for products.
Optimized Sorting Station:
Sorting productivity is optimized with LED guidance and drop detection systems, as well as voice-guided assistance. Despite the additional product handling, overall productivity is doubled. The workstation and software ergonomics were customized in collaboration with the client to reduce the strain on workers.
The LED system is highly effective and interesting: it allows only the products to be picked to be lit up. The operator almost no longer needs to use their scanner. We really found the product—both hardware and software—highly efficient in boosting the productivity of the picking process.
Director of La Colle sur Loup
The Advantages of Pickeos
Efficient IT Integration: Pickeos worked closely with the IT provider integrated with E. Leclerc to develop a high-performance software solution aimed at optimizing the drive-thru operation.
Quick Return on Investment: “The investment is not very high, but we double the productivity: the return on investment is very quick.” – Mr. Mailfert, Director.
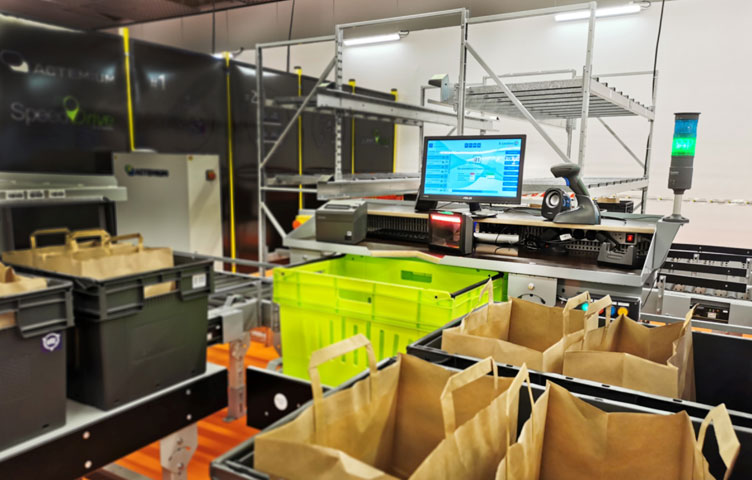
Results and ROI
+50%
productivity
20X
fewer steps for operators
1 jour
of training instead of 1 week
Need a demonstration?
If you need more information, a presentation of Go-to-Light, or a quote…
We are available to answer all your questions.